OK. Today's topic is related to the work experience [previously I've been in this field] :)... I worked as Digital Pre-Press Operator for five years at two different company in CTP Department or Computer-To-Plate. Other than skills in computer, it also requires expertise in the field of designing and graphics printing operations. In addition, must have experience in how a substance's books or magazines made. Basically, it starts at the design and Desktop Publishing stage then sent to the Digital Pre-Press stage prior to the printing process.
1. Each material before it became a book or magazine, it must first undergo the process at Desktop Publishing (DTP). At this stage, graphic designers will ensure that the concept has a unique attractiveness, orderly and neat. Graphic Designer will also determine the position of typography and images included. Images must be 150 dpi (Dot Per-Inch) above and CMYK formats. Examples of DTP software are Adobe In-Design, Pagemaker, Quark Express and many more.
2. Based on experience in this field, Digital Pre-Press department choose to receive a file in the *.pdf format. It's easy and simplify the process of Refining. However, this process will run well when preparing the *.pdf proper and correctly. An example software of the refining processor is Prinergy by Creo.
*.pdf - Portable Document Format. Developed by Adobe Systems, this format allows document that are created in any program to be converted to PDF format which can then be "read" by the free Adobe Acrobat Reader software, regardless of whether the originating software used to originally create the document is available on the viewers computer. PDF files can be created from most programs by using the Adobe Acrobat software.
3. Refining is a process where the *.pdf files examined by several criteria that have been determined or called Pre-Flight (The process of checking DTP files before output by the output provider, in order to check if the files will run successfully on the imagesetter. In pre-flight, the files are not actually output on an imagesetter. Files may be opened and examined and/or run through a checking or imagesetter-emulation program). For example, the system will detect if there any images less than 150 dpi or fonts are not embedded. So, if any, further actions will be taken either get new files or repair the existing, depending on the discretion and evaluation.
4. Before proceed to layout process, Digital Pre-press Operator will check each file, page by page accordingly. Yes, make sure all bleeds are enough at least 3mm away from the trim size, this facilitates the process of cutting stage. Further, identify the any missing images, fonts not embedded, size of book / magazine as requested, make sure files are complete and more...
5. The next step is the layout or impositioning. I can say that this stage is quite difficult. It requires focus and it depends strongly on the Job Plan that has been provided. There are some companies call it Job Plan, Job Sheet, Work Sheet, and more. Depending on the comfort and work culture. So here are two important things that should be emphasized. First, related to Impositioning and the second is Job Plan.
6. In the process of Impositioning, it is dependent on the Job Plan. Position of every page based on paper print size width, height and how it folds. Normally the number of pieces in a single surface is 8 pages. Once again, it depends on the size of paper, printing and folding machines. If the book will be completed in the form of, for example Saddle Stitch (Stapled), then the way it folds and position page also different.
Impositioning Software - Signastation
Set the position of each page.
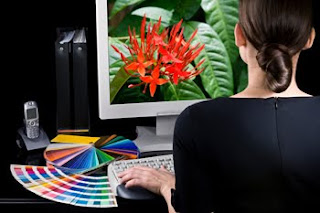
Here, I will list briefly the process of making a book or magazine:
1. Each material before it became a book or magazine, it must first undergo the process at Desktop Publishing (DTP). At this stage, graphic designers will ensure that the concept has a unique attractiveness, orderly and neat. Graphic Designer will also determine the position of typography and images included. Images must be 150 dpi (Dot Per-Inch) above and CMYK formats. Examples of DTP software are Adobe In-Design, Pagemaker, Quark Express and many more.
2. Based on experience in this field, Digital Pre-Press department choose to receive a file in the *.pdf format. It's easy and simplify the process of Refining. However, this process will run well when preparing the *.pdf proper and correctly. An example software of the refining processor is Prinergy by Creo.
*.pdf - Portable Document Format. Developed by Adobe Systems, this format allows document that are created in any program to be converted to PDF format which can then be "read" by the free Adobe Acrobat Reader software, regardless of whether the originating software used to originally create the document is available on the viewers computer. PDF files can be created from most programs by using the Adobe Acrobat software.
3. Refining is a process where the *.pdf files examined by several criteria that have been determined or called Pre-Flight (The process of checking DTP files before output by the output provider, in order to check if the files will run successfully on the imagesetter. In pre-flight, the files are not actually output on an imagesetter. Files may be opened and examined and/or run through a checking or imagesetter-emulation program). For example, the system will detect if there any images less than 150 dpi or fonts are not embedded. So, if any, further actions will be taken either get new files or repair the existing, depending on the discretion and evaluation.
4. Before proceed to layout process, Digital Pre-press Operator will check each file, page by page accordingly. Yes, make sure all bleeds are enough at least 3mm away from the trim size, this facilitates the process of cutting stage. Further, identify the any missing images, fonts not embedded, size of book / magazine as requested, make sure files are complete and more...
5. The next step is the layout or impositioning. I can say that this stage is quite difficult. It requires focus and it depends strongly on the Job Plan that has been provided. There are some companies call it Job Plan, Job Sheet, Work Sheet, and more. Depending on the comfort and work culture. So here are two important things that should be emphasized. First, related to Impositioning and the second is Job Plan.
6. In the process of Impositioning, it is dependent on the Job Plan. Position of every page based on paper print size width, height and how it folds. Normally the number of pieces in a single surface is 8 pages. Once again, it depends on the size of paper, printing and folding machines. If the book will be completed in the form of, for example Saddle Stitch (Stapled), then the way it folds and position page also different.
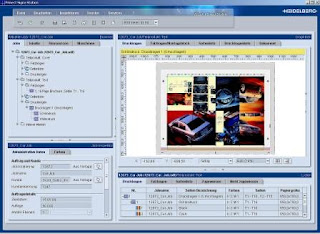
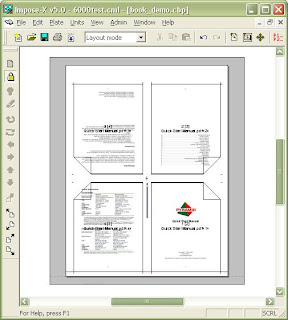
8. The completed Imposition also known as Signature. Now, after the position is determined, place each PDF file that has been processed into the Signature. Place the PDF by following the trim marks accordingly or just place it in the middle.
9. After Impositioning made, prior to the preparation of plates, each first impositions just need to print out Ozalid. Ozalid act as a print view, similar to the actual printing. It is also a pre-view to see the entire book / magazine to be produced. Here, the editor or designer will check every spelling, colors, layout, design and type of binding is correct, and also some other criteria.
10. After Ozalids have been confirmed by the editor or publisher, thus the impositions will be published in the form of plates. Plates or Printing Plates is printing processes such as offset lithography use printing plates to transfer an image to paper or other substrates. The plates may be made of metal, plastic, rubber, paper, and other materials. The image is put on the printing plates using photomechanical, photochemical, or laser engraving processes. The image may be positive or negative.
11. So, in the Plate Division, the operator will produce plates based on color. If the book / magazine is in CMYK, then plate is produced by 4 pieces for each side of imposition. Means, one color one plate. If there any additional color other than CMYK, then it is known as a special color or colors that have been selected in accordance with the design, for example Gold color, Silver color, Pantone colors and more.
9. After Impositioning made, prior to the preparation of plates, each first impositions just need to print out Ozalid. Ozalid act as a print view, similar to the actual printing. It is also a pre-view to see the entire book / magazine to be produced. Here, the editor or designer will check every spelling, colors, layout, design and type of binding is correct, and also some other criteria.
10. After Ozalids have been confirmed by the editor or publisher, thus the impositions will be published in the form of plates. Plates or Printing Plates is printing processes such as offset lithography use printing plates to transfer an image to paper or other substrates. The plates may be made of metal, plastic, rubber, paper, and other materials. The image is put on the printing plates using photomechanical, photochemical, or laser engraving processes. The image may be positive or negative.
11. So, in the Plate Division, the operator will produce plates based on color. If the book / magazine is in CMYK, then plate is produced by 4 pieces for each side of imposition. Means, one color one plate. If there any additional color other than CMYK, then it is known as a special color or colors that have been selected in accordance with the design, for example Gold color, Silver color, Pantone colors and more.
After all plates are ready, it will be sent to the Press Department for printing!
About like that lar! What else you want to? Hehehe ...!
Much remains to be shared ... just enough so far ... later you dizzy! This is just only 50% of the overall process in the CTP! These are too basic I guess :)
I hope you have some information about the CTP and early production of books / magazines ... which is also called Pre-Press Production!
Cheers!
By
Wel Loren
About like that lar! What else you want to? Hehehe ...!
Much remains to be shared ... just enough so far ... later you dizzy! This is just only 50% of the overall process in the CTP! These are too basic I guess :)
I hope you have some information about the CTP and early production of books / magazines ... which is also called Pre-Press Production!
Cheers!
By
Wel Loren
0 comments:
Post a Comment